EUROPA PRESS
La tecnología española convive con herramientas procedentes de otros países europeos como Alemania
HARBIN (CHINA), 23 Sep. (EUROPA PRESS) -
El consorcio aeronáutico Airbus ha reforzado su apuesta por China y así lo ha demostrado con la inauguración de un nuevo centro de finalización y entrega del modelo A330, localizado Tianjin, una factoría que se une a los centros ya existentes en las ciudades de Pekín, Tianjin y Harbin.
En esta última ciudad, Harbin, ubicada en la zona noroeste del gigante asiático y en la que en invierno los termómetros pueden llegar a marcar 30 grados bajo cero, Airbus y sus socios locales, HAIG, HAI, AVICHINA y HELI, que operan bajo el nombre Harbin Hafei Airbus Composite Manufacturing Centre, trabajan desde 2009 para producir piezas y componentes de material compuesto para su modelo A320 y desde 2011 también para el A350.
La presencia española y europea en este centro se hace notar, tanto en la composición de su plantilla como en la tecnología que utilizan.
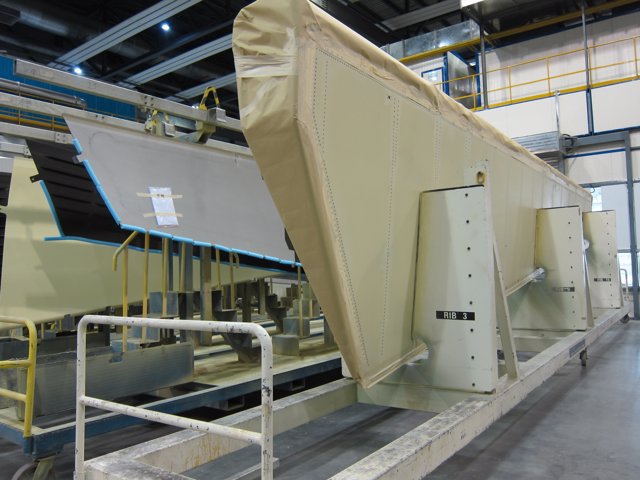
Concretamente, en esta fábrica participada en un 29% por Airbus, se producen las piezas del panel ventral de los aviones, los timones de profundidad y los timones de dirección, unos componentes que, una vez finalizados, son enviados a los clientes de Airbus de Europa y Asia para que estos sigan avanzando en la cadena de producción y montaje antes de pasar al último paso: el del ensamblaje final y su posterior entrega a las aerolíneas o compañías de alquiler de aviones.
En estos momentos el centro de fabricación de Airbus en Harbin cuenta con una plantilla de unos 700 empleados, entre los que se encuentran unos 10 expertos españoles además de otro grupo de ingenieros de distintos países europeos. Desde Airbus indican que el número de especialistas provenientes de factorías europeas en esta planta china se ha ido reduciendo desde su creación, y que, siguiendo su política, su presencia seguirá disminuyendo a medida que los profesionales locales adquieran la autonomía suficiente para llevar a cabo la producción total.
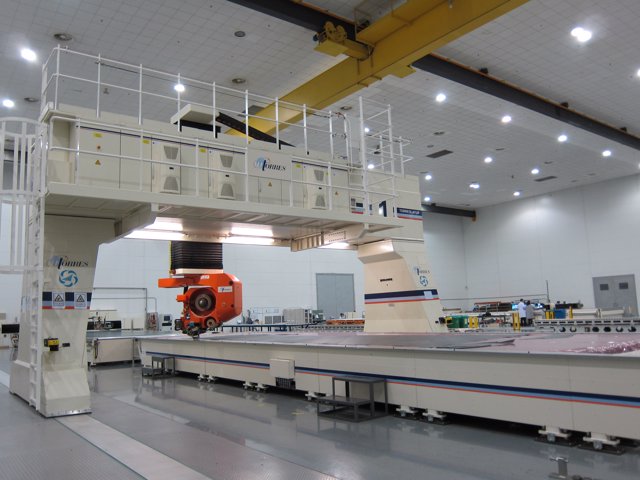
PRESENCIA DE MARCAS ESPAÑOLAS.
Aquí, tecnologías de última generación como la de la máquina herramienta de la compañía navarra Mtorres, especializada en la automatización de procesos industriales de alta complejidad, capaz de dar forma a los timones de dirección y profundidad de los aviones en fibra de carbono, conviven con la fabricación manual de otros componentes de este mismo material.
Además de la máquina herramienta de Mtorres, en el interior de la factoría de Airbus en Harbin se encuentran grúas de Serra, una empresa catalana experta en la tecnología de ensamblaje y la soldadura y máquinas industriales de la empresa 100% española Deltavigo, así como una máquina de termoconformado de la vasca Fagor.
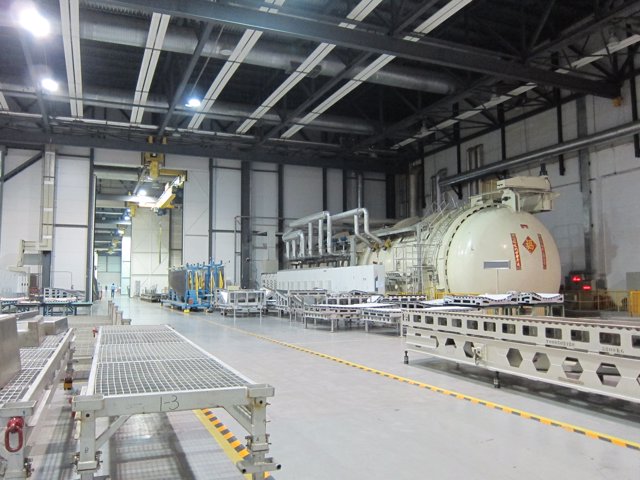
"Hay muchas máquinas españolas", explica uno de los ingenieros del equipo europeo que trabaja en la planta, Antonio Pelliciotta. La tecnología española convive con herramientas procedentes de países europeos como Alemania y con tecnología china como la que se aplica en el autoclave, un horno industrial que permite que, una vez finalizada su producción en carbono, las piezas se fijen y se doten de la resistencia necesaria. "Tenemos tecnología de todo el mundo, es un 'mix'", apunta el ingeniero.
Pero además de en las instalaciones, España también está presente en el centro de materiales compuestos de Airbus en Harbin Hafei por otro motivo: dos importantes clientes son empresas españolas. Se trata de la andaluza Alestis y Aernova, otra de las grandes proveedoras de estructuras aeronáuticas de la compañía europea y responsable de los estabilizadores horizontales de cola del modelo A350.
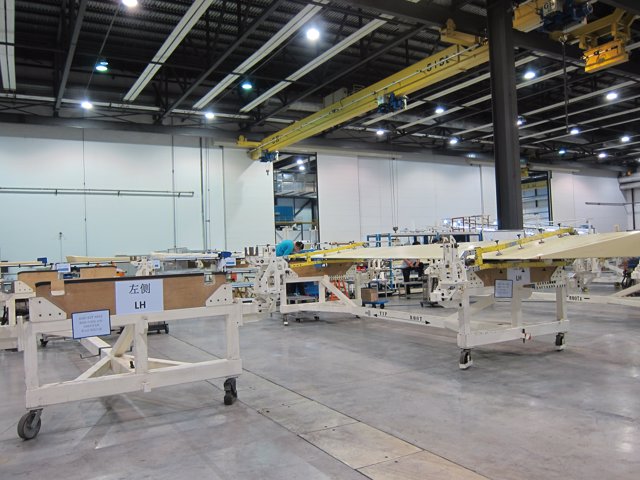
Estas compañías españolas, como los demás proveedores del consorcio, siguen con el recorrido de la cadena de producción y cuando finalizan sus trabajos, envían las piezas resultantes a la sede de Airbus en Toulouse, (Francia), donde se encuentran las líneas europeas de ensamblaje final de la multinacional y desde dónde, una vez ensambladas en los aviones, pueden empezar a volar.
LA ARTESANÍA SE CUELA EN EL PROCESO INDUSTRIAL.
En el proceso productivo, cada pieza suele durar alrededor de dos meses desde el momento en el que se inicia hasta que la pieza llega al cliente, se conjugan tecnología puntera y trabajo artesanal.
El trabajo artesanal se lleva a cabo en una sala especial en la que se reúnen las condiciones necesarias de higiene. Aquí, un grupo de expertos crea con sus propias manos las piezas de carbono del panel ventral del modelo A350. El proceso es largo y requiere un alto nivel de especialización. Cada empleado dedica una jornada (ocho horas) a la creación de un único panel.
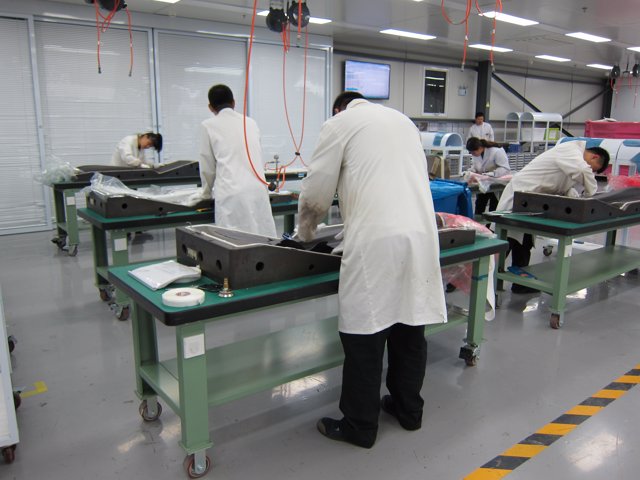
"Es un trabajo muy delicado", explica Pelliciotta. Este profesional italiano asegura que para realizar la labor manual se requiere un alto grado de especialización y destaca que es la dificultad para dar la forma a la pieza la que motiva que se produzca sin la intervención de máquinas.